Utilising trenchless, no-dig technology for drainage maintenance
7 October 2020
Trenchless techniques – also known as ‘no-dig’ methods - are increasingly used in the construction industry. There are multiple reasons for their growing popularity and, in the context of industrial drainage maintenance, they are considered best practice wherever the option is feasible.
What are trenchless techniques?
As the ‘no-dig’ term suggests, trenchless techniques provide an alternative to the traditional excavation which used to be prevalent in the maintenance of underground structures such as drainage networks. The latter is an open-cut method which usually involves digging up and replacing pipework, whereas the former leaves the ground untouched and requires only a few access points (e.g. manholes) to reinforce existing pipes, with all remedial work carried out underground. Pipes are prepared for renovation using high-power jetting.
What benefits do trenchless techniques offer compared to excavation?
In comparison to excavation, trenchless techniques are far more practical as well as making better financial sense and better environmental sense. There are various compelling reasons to opt for a no-dig solution.
1. Less Disruption
Compared to invasive excavation, trenchless technology has a much lower impact on the surrounding environment – topographically, ecologically and socially. Because most of the work occurs underground, trenchless methods only need a few access points, containing the disruption to specific locations. Minimal surface disruption means that roads, business districts, industrial sites and residential areas remain largely unaffected. Taking digging out of the equation decreases the length of time required to rehabilitate the work area to as-found or better condition. The footprint is smaller for a trenchless construction zone and its fast turnaround time reduces the inconvenience associated with construction projects.
2. Reduced cost
Some estimates say that trenchless techniques save up to 50% in cost compared to traditional excavation methods, which require longer preparation, more workers and more equipment. The financial impact on the wider area is also a vital consideration and this is where the quicker turnaround and minimal disruption of no-dig solutions can dramatically reduce expense. For businesses operating on site, it means reduced downtime on their premises. In a retail environment, it means reduced impact on footfall. Commercial districts can plan no-dig maintenance to avoid loss of revenue. This can make a huge difference to cost savings in comparison to the more prolonged disruption of excavation. The government has estimated that road closures cost the UK economy approximately five billion pounds each year.
3. Increased Safety
Safety is paramount in construction projects and excavation is a relatively high-risk technique. As well as posing a danger of landslides and related accidents, open-cut excavations can come into contact with ‘unknowns’ below ground, including harmful chemicals or unsecured electrical wires. The more controlled methods of trenchless technology enable a much higher level Health & Safety.
4. More eco-friendly
The reduction in disturbance enabled by do-dig technology includes a reduction in ecological disturbance. Rural areas can be kept intact, an especially important factor if they contain protected wildlife habitats. Trenchless methods also lower the carbon footprint as they reduce manpower, transportation of equipment and energy consumption in comparison to traditional excavation. Noise and air pollution are minimised. No-dig remediation also prolongs the lifespan of existing materials, using broken or damaged piping as a skeleton for new pipe lining, so old pipes are not discarded unnecessarily. This impressive combination of environmental benefits brings impeccable green credentials to construction and maintenance projects.
5. Improved Accuracy
It’s often assumed that, without excavating and laying bare the location of a fault, trenchless techniques are less accurate in their diagnosis and remediation. This assumption is wholly mistaken – with the use of CCTV surveys, which insert CCTV cameras into drain lines, trained operatives can apply a method of exploration comparable to keyhole surgery, identifying exact locations of any issues and compiling accurate reports based on the footage. In contrast, excavation methods disturb the area around a fault and potentially make accuracy more problematic.
Examples of trenchless techniques
Various trenchless techniques are commonly used to avoid excavation in the maintenance of drainage networks. These include Cured in Place Pipe (CIPP) patches and CIPP lining. Before these remedial methods are applied, it is important to investigate the precise location and extent of any necessary work. This can be achieved through CCTV surveys, providing a real-time view of drain conditions which is fed back for observation and analysis. The results of this analysis usually determine whether the most suitable solution is CIPP patching or CIPP lining.
1. CIPP patching
CIPP patching is suitable for 75-1500mm diameter pipes and is often the most appropriate solution for localised or isolated damage such as small cracks or unstable joints. The patch is manufactured from glass fibre matting and coated in resin. The matting is rolled around a “packer” which is inserted into the pipe and inflated to push the patch against the pipe and bond with its surface through curing. Once the patch is cured, the packer is deflated and removed.
Advantages
- Excellent structural strength.
- Versatile application (patches can be installed sequentially in the middle of a pipeline).
- Zero shrinkage.
Disadvantages
- To avoid rain or solar heat, the wet-out (application of resin) must be done under shelter.
- It can be difficult for rigid packers to access larger diameter pipes.
- Manual handling is cumbersome for larger patches.
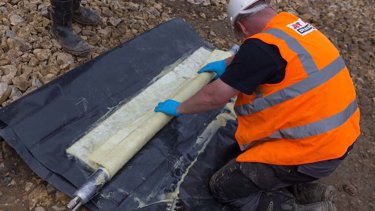
2. CIPP lining
CIPP lining is more suitable when a CCTV survey reveals multiple issues, too numerous to be addressed with localised patches. In these cases, it is usually more efficient and cost-effective to install a liner. CIPP lining can be applied through three different methods of curing: hot, ambient or ultra-violet.
Hot cure
Hot curing is a common method recognised by Water Industry Specifications WIS 4-34-04 or BS EN ISO 11296-1-2011. A resin-impregnated liner is inserted into the pipe and pulled through from one manhole to the next. The liner is filled with water which is heated to around 85 degrees and circulated for 4 hours until the liner cures in place. The water is left to cool and is released with the cutting and trimming of the liner. It is unsuitable for surface water drains due to styrene emissions.
Advantages
- Adaptable solution that can accommodate bends of up to 45 degrees.
- The controlled cure makes it ideal for long drain runs.
- Has a design life of 50-100 years and can utilise epoxy or vinyl ester resin to increase chemical resistance.
Disadvantages
- Compared to other lining methods, it often requires a larger site footprint for installation.
- Heating process is less energy-efficient than other methods.
- Curing process produces wastewater contaminated by marine pollutants (styrene) which must be removed and properly disposed.
Ambient cure
Ambient cure lining uses a type of epoxy that cures much faster than the standard mixture and does not require heat or much extra equipment. It may begin to cure during installation, which means its suitability is limited by the size of the liner. The resin-impregnated liner is cut to length and installed using a compressor and an inversion drum.
Advantages
- Faster installation and ideal for managing existing flows.
- Can be carried out from one access point, with smaller site footprint and minimal labour.
- Adaptable solution that can accommodate bends of up to 90 degrees.
Disadvantages
- Only suitable for shorter runs of 100–150mm diameter pipes.
- A non-structural solution.
- Minor shrinkage is possible.
Ultra-Violet
Ultra-Violet (UV) curing is increasingly the preferred method for CIPP lining. The liner is impregnated with light-sensitive resin. The liner is inflated with air and UV light train is then pulled through the run. The light cures the sewer lining on contact, providing a fast installation. Unlike heat curing, it has no styrene emissions and does not produce contaminated wastewater, making it suitable for surface drains. The lightweight and portable equipment used during UV curing makes it easier to carry out work on challenging sites and inaccessible areas.
Advantages
- Smaller site footprint, faster installation and less labour intensive
- Liners are thinner yet stronger, minimising the reduction in the cross section of a pipe.
- Reduced energy consumption and carbon footprint.
- Can be used on lines with multiple bends and diameter changes and were a “blind shot” is needed
- Greater variety of liners for every application
Disadvantages
- Can be unsuitable for remediation of severely fractured drains as there is a risk of damaging the liner.
- Requires a greater investment than other options.
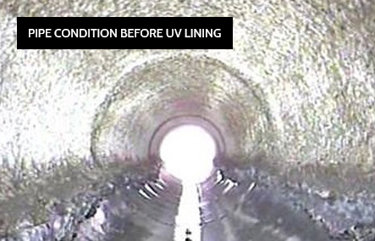
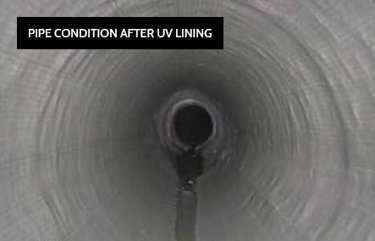
Using trenchless methods in planned maintenance
When drainage issues become evident, the ideal solution is a CCTV survey followed by the most appropriate trenchless technique. This process is the most effective and efficient form of reactive maintenance, but in the longer term it is even more useful to apply it as part of a planned maintenance programme – in other words, to identify potential problems and avert them before they become evident.
Periodic CCTV surveys can provide drainage health checks which reveal faults in their infancy and address them before they advance to a more serious state of deterioration, preventing a much more severe impact further down the line and making huge cost savings as a result. No-dig techniques are renowned for minimising disruption, but harnessing them with a forward-thinking approach to maintenance is the best way to make full use of this advantage.
For expert advice on trenchless drainage maintenance, please contact our team of specialists.
Here to keep your drainage flowing freely
Our experts are available to quickly diagnose issues, provide cost-effective solutions, and carry out routine maintenance to get your drainage network back to normal as soon as possible.
Speak to our experts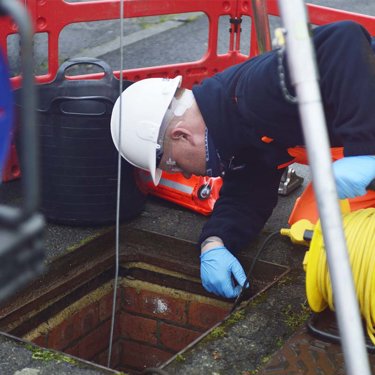